Vector.ucaldas.edu.co
Vector 10 (2015) 59 - 64
Design of a production plant of LDPE in Colombia
Cristian Felipe Jimenez-Varon1*, Reinel Tabares Soto2
1 Engineer. Professor, Department of Maths and Statistics, Universidad Nacional de Colombia, Manizales
2 Engineer. Professor, Department of Electronic and Automation, Department of Maths and Physics, Universidad Autonoma de Manizales, Manizales
Recibido: 28/09/2015. Aprobado: 05/12/2015.
Abstract
The present article is a study on the production of polyethylene as a product of the polymerization reaction of ethylene monomer, a
thorough analysis of its production, raw materials and catalyst required to carry out this reaction. The study begins by inquiring about
generalities on the compound, physical and chemical properties, and current industrial applications.
Key words : Polyethylene, ethylene, polymerization, monomer, tubular reactor.
Diseño de una planta de LDPE en Colombia
Resumen
El presente artículo es un estudio sobre la producción de polietileno como un producto de la reacción de polimerización del monómero de
etileno, un análisis exhaustivo de su producción, materias primas y del catalizador necesario para llevar a cabo esta reacción. El estudio
comienza por preguntar sobre generalidades sobre el compuesto, propiedades físicas y químicas y aplicaciones industriales actuales.
Palabras clave: polietileno, etileno, polimerización, monómeros, reactor tubular
presence of a reaction initiator and thus produces
tubular reactors polyethylene, low density.
Polyethylene is made from a raw material derived
from petroleum: Ethane, and subsequently by reacting,
Production and Characterization
ethylene monomer catalytic cracking is obtained.
The reaction for obtaining ethylene cracking is
The polyethylene in the market is produced at a
carried out at high temperatures and special conditions cost of between US $1200/t and US$ 1800/t, the average
of pressure.
annual world production is 80 million tons, which
Once the ethylene is obtained through a reaction of are directed to various processing industries where
appropriate ethylene polymerization, several chains of polyethylene is used for molding processes such as
ethylene are formed. This polymer has properties and blow types, compression transfer, among others,
diversity of changes in pressure and temperature used for various applications where the polyethylene is
in the processes.
Polyethylene is an olefin, a member of the family of
The production plant of LDPE, was modeled for
thermoplastics. The raw material for the manufacture is the production of about 12 t/h, from a feedstock flow
high purity ethylene produced from ethane flows, from of 65 t/h of ethylene entering a compressor in order
the gas oil cracking process, which in the Colombian to rapidly increase the pressure before entering the
context is currently produced by the Ecopetrol industry reaction zone.
(Martin, 2005).
The main physical characteristics that contain the
The high purity ethylene is subjected to high main information of each compound, including the
pressure and temperature for polymerization in the principal raw material and product characterization
that will be obtained, were found in Malppas (2012).
* Autor de correspondencia.
[email protected] (CF Jimenez Varón)
Cómo citar este artículo:
Jimenez-Varon C.F., Tabares Soto R. (2015). Design of a production plant of LDPE in Colombia.
Revista Vector, 10: 59-64.
Cristian Felipe Jimenez-Varon, Reinel Tabares Soto / Vector 10 (2015) 59-64
radicals, for our process, benzoyl peroxide and
Di terc butyl peroxide were used as substances
Currently the only producer of LDPE in Colombia for the initiation of the reaction. Polyethylene
is the Ecopetrol business group, which has two production requires a source of pure ethylene, suitable
production plants, one in Cartagena and the other compression equipment to operate at about 2000 bar,
in Barrancabermeja. Ecopetrol Business Group is the and a high pressure reactor to perform quick and high
greatest supplier of raw material, and has high levels exothermic polymerization control. The process takes
of production of this requirement, the plant plans to place in continuous operation.
build and operate in the municipality Puerto Colombia
The process of production of LDPE, basically has
located in the Atlantico department due to this town three key stages (see Figure 1) which are: Pretreatment,
is near to the plant ecopetrol and it is a strategic site an essential step to adapt the conditions of pressure and
given its port as an enabler to export polyethylene in temperature of the stream prior to entering the reaction
the form of raw material (APCA, 2013).
zone commodities, this stage consists of equipment
The location of the plant is chosen by the ease and such as compressors and heat exchangers, which ensure
efficiency improvement in the processes of internal that the flow of the ethylene and the initiators being
and external logistics regarding acquisition of raw introduced in the reactor of polymerization are at least
materials and distribution of products and in terms 2000 bar and about 150 degrees centigrade. The second
of transportation costs, distribution and cellar times key step is the reaction zone, this process is modelled
of both raw materials and products.
in high pressure tubular reactors, which has a water
vapor stream to ensure the temperature conditions in the
reactor, the plant as a reaction zone is subdivided into
four subzones, since injection points are the initiators for
One of the beneficiaries of this project are the the start of reaction mechanism. The final part is the area
petroleum businesses, since they would have a large of separation, consisting of a Flash equipment, which
customer demand for its products as raw material, evaporates the amount of ethylene that do not react and
produced as a product of petroleum. Also, there are then it is used in recirculation but also in the current
industries getting benefits from the prosecution of obtained from the product (Textos Científicos, 2005).
plastic to finished products requiring the LDPE as raw
material, not only in the national context, just as Riduco
Reactor Operation
in the city of Manizales, but in the international context
as well. All of this due to LDPE is the most widely used For this part of the process, an exhaustive review of the
polymer in the thermoplastic industry worldwide for literature was carried out, from which the following
conclusions were addressed: The polymerization
The following companies are currently the largest reaction occurs by a kinetic chain reaction mechanism
producers of plastic in the global market based on by free radicals, consisting of 10 semi-reactions (Odian,
sales of chemicals: BASF, Germany Dow Chemical, 2004).
USA INEOS Group, LyondellBasell England, and
Netherlands ExxonMobil, USA SABIC, Saudi Arabia · The tubular reactor is a PFR in countercurrent,
DuPont, USA Total, France Formosa Plastics Group,
countercurrent PFR, divided into 4 sections due
Taiwan Bayer and Germany (C&EN, 2014).
to the injection of the initiators of the reaction
Given that the plant that uses different resources
derived from petroleum, this production would
increase the commercialization of these derivatives · The reactor operating temperature is between 150-
for various applications which would increase the
development, and the economy of the country.
· The reaction works at high pressures in a range of
2. Methods and Structure of process
2000-3000 bars.
· The length of the reactor is about 1000 m.
Process Basic Structure
· The internal diameter of the tubular reactor is in a
Polyethylene is produced from the polymerization
range of 25-50 mm.
of ethylene. The polymerization reaction is sensitive
to a very large number of catalysts and it is initiated · Conversion reactor is quite low for the process,
particularly easy by compounds that produce free
about 20 % (Cuevas, 2012).
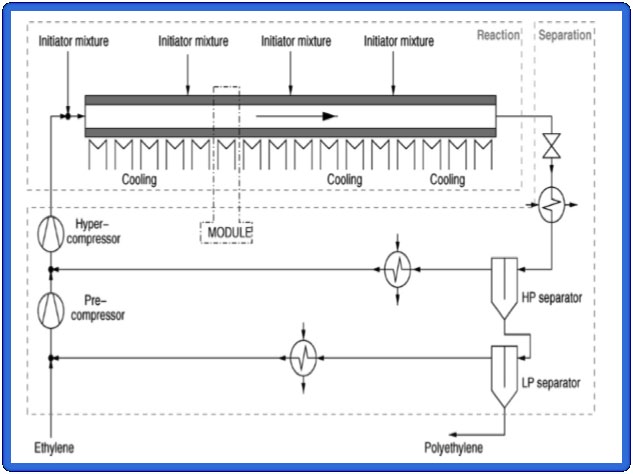
Design of a production plant of LDPE in Colombia
Figure 1. Flow-sheet of the LDPE production plant (Textos Cientificos, 2005).
3. Process Description
The reaction zone is conducted by a mechanism of Ethylene Pre-treatment
reaction of 10 reactions (Kienle et al., 2005).
The reaction rate constants (k) are represented by
The ethylene required as input into this process
modified Arrhenius equations (Kienle et al., 2005); is transported in tankers to withstand high pressure
including the effects of temperature (T), change of liquid inflammable from the supplier company,
pressure and Activation Energy:
Ecopetrol. This is acquired and deposited in a storage
tank at atmospheric conditions before entering to the
process (Ecopetrol, 2014).
After it enters the process, it is initiated in the
conditions of pretreatment to have the raw material
prepared before being in the reaction zone.
Here K is the frequency factor specified for each
The ethylene stream is required to be pressurized
reaction, the term
is the activating thus it enters a compressor prior the reaction zone.
Energy, IR the Gas constant and T is the temperature.
After the content of ethylene stream is pressurized,
The kinetics for the reactions is of first order, the it is split into two streams: The first one is going to
kinetics parameters were found in (Brandup, 1989).
react to the first two reaction zones with injection of the
The reactor is the central body in the production initiators, and this must react at a higher temperature.
process, this works continuously, therefore the
The second stream enters another heat exchanger
injection of the initiators should always be listed in each that should be operated at a lower temperature and also
section of the reactor, and the tubular reactor shall keep enters the mixer with the injection of new initiators in
its conditions of temperature, pressure and condition addition to the current coming from the reaction zone
of phase to the reactive mixture, so that the kinetic rate 2. The mixture has to be carried out before entering the
laws and reaction mechanisms are not affected (Dong reaction zone 3 and 4.
and Piet, 2004).
Different points in the reactor have steam inlets Reaction
in order to maintain an appropriate temperature and
pressure conditions; this steam is supplied by a boiler
The reaction process is carried out in PFR tubular
producing it at medium pressure.
reactors, where a reaction mechanism of PCR is
performed; this is subdivided into 10 reactions or
Cristian Felipe Jimenez-Varon, Reinel Tabares Soto / Vector 10 (2015) 59-64
steps in the various stages of the mechanism, such of ethylene that does not react and is evaporated in
as initiation, which generates free radicals that will the Flash separator. The reagent that does not react
link with different chains of ethylene, forming a vinyl is carried out to some storage tanks, which have to
polymer. Then at the stage of propagation different enter a purification process before returning to the
transfers of radical and monomer occur in order to starting point.
gradually increase the number of chains formed.
The storage tank must have hermetic conditions to
Finally, the polymerization process is completed by maintain the pressure and temperature for the ethylene
temperature conditions that disrupt the chemical stream.
bond formed, producing low density polyethylene
in the temperature range established for the reaction
4. Results
(Idarraga, 2010).
LDPE is polymerized forming large chains and Simulation Process
generating enough entropy in the order of their bonds
between monomers, causing a reduction of their
The project was carried out using a process of
density given that the internal structure has different simulation tools. The objective of this procedure was
types of defects (Donald et al., 2004).
to generate the mass and energy balances from which
raw materials were required. The utilities and energy
Specifying the fluid service
needs are calculated.
The main simulation tool used was the commercial
In order to preserve the conditions of the reaction, package Aspen Plus V8.0.
specify and justify the operating conditions, reactors
The method of calculation of the properties for
should have a thermal fluid service, which for our the polymerization process is known as the Sanchez-
case is water.
Lacombe equation, also known as the basis Polysil
method in the Aspen Plus software.
Sanchez-Lacombe equations are few models used to
calculate thermodynamic properties of liquid solutions
In the design of the production plant of LDPE, there for polymers (Dimitrios et al., 2011).
are two separators: Flash isothermal type, located at the
exit of the reaction zone 4, which is used to reduce the Sanchez-Lacombe Equation State
pressure to an intermediate value at the atmospheric
pressure, in order to carried out Flash separation is
The equation of state of Sanchez and Lacombe
(1976), is based on the theory of crosslinked flow,
assuming that the polymer has a liquid structure
· A total mass balance.
flexible. This limits the use of this equation a non-
· A mass per component balance.
crystalline polymer. This equation is also used to
· A total energy balance.
model the solubility of supercritical CO2 in solid and
amorphous and molten polymers. It also describes
The first Flash separator works at high pressures; the subsequent swelling of the polymer when the FSC
the second Flash separator works at lower pressures in the polymer dissolves. Three considerations are
(Lipatov and Nesterov, 1998).
necessary when Sanchez-Lacombe equation is used:
In the Flash 1, the liquid phase contains the 1. The solubility of gas in the polymer represents a
monomer and polymer, whereas the gas phase is a balance data, 2. the solubility of the polymer in the
recycle stream since it is not a product. Ethylene by stage of high pressure gas is essentially zero and
itself does not react.
3. Amorphous polymer about its glass transition
The Flash 2 is assumed as an ideal separator for temperature can be modeled as a liquid (Rozzi and
polymer-monomer mixture, the monomer is recycled Singh, 2006).
to the process and the polymer is removed from the
Table 1. Simulation results.
Treatment of ethylene recirculation
Due to the low conversion in the polymerization
Ethylene For Recirculation
reaction that produces polyethylene, the large amount
Polyethylene (LDPE)
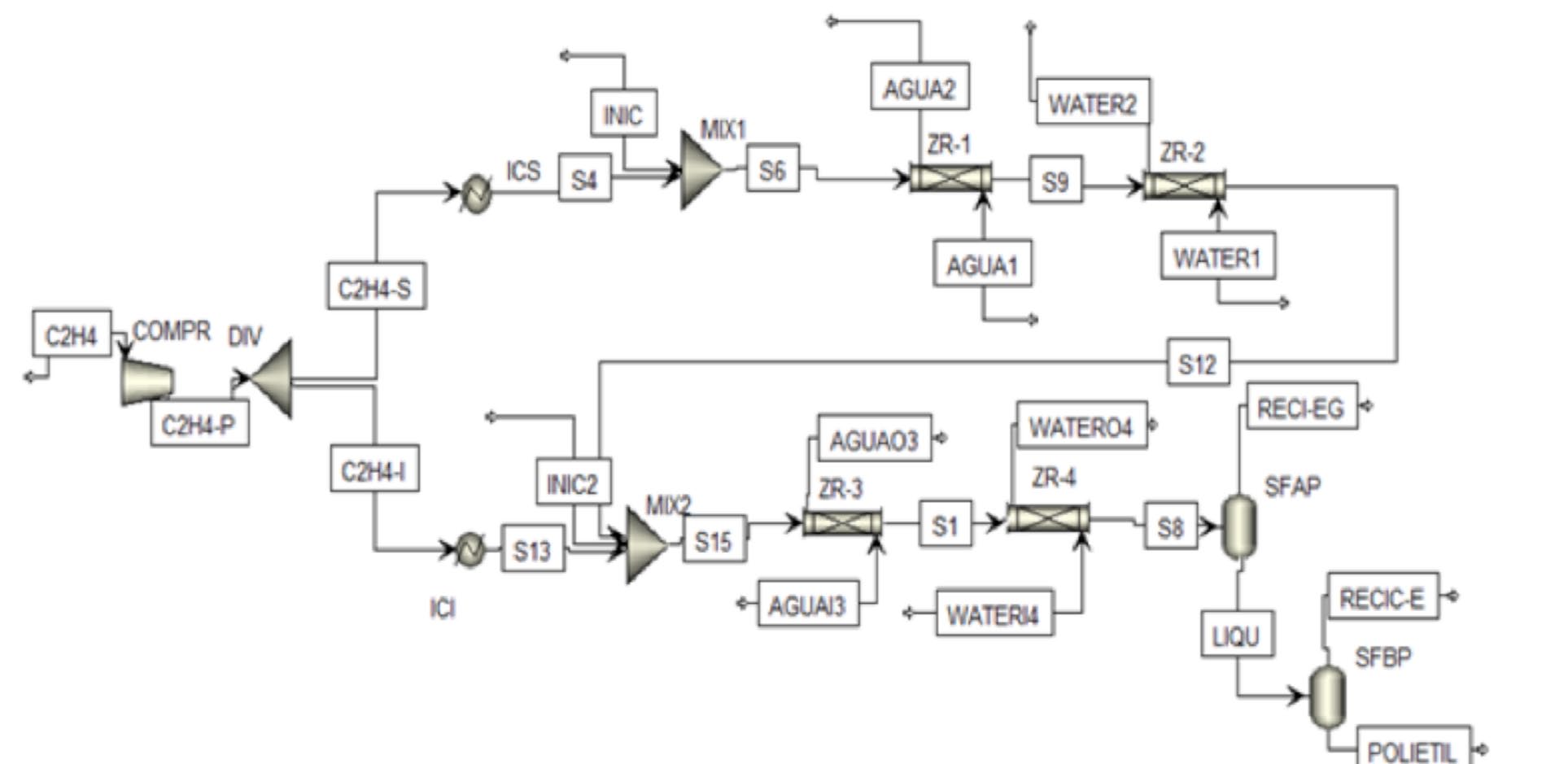
Design of a production plant of LDPE in Colombia
Figure 2. Scheme process for LDPE production.
Environmental analysis of the production of LDPE
this project.
The environmental analysis developed in WAR-
The environmental analysis was performed with the GUI required:
help of software WAR-GUI, which is an algorithm that
analyzes the conditions and environmental impacts · Flow rate and composition of each in and out
of the project from 8 different categories (EPA, 2011).
stream of the process.
The environmental potential impact was defined as
the effect that could have on the environment emissions · Rate of energy consumption.
of gases such as ethylene and others that are part of
Figure 3. Environmental impact by the formation of smog.
Cristian Felipe Jimenez-Varon, Reinel Tabares Soto / Vector 10 (2015) 59-64
As noted in Figure 3, the environmental impact is Dimitrios M., Prokopis P., Apostolos B., Costas K. (2011). Prediction
largely marked by the formation of smog, aquatic and
of the molecular and b polymer solution properties of LDPE in a
high-pressure tubular reactor using a novel Monte Carlo approach.
Chemical Engineering Science, 66: 1685-1696.
It must be taken into account that a process that Donald A., Pradeep P. Phulé. (2004). Ciencia e ingeniería de los
uses raw materials derived from petroleum has high
materiales. Thomson Editores: México. 1003 p.
emissions of carbonic gas into the atmosphere. Caution Dong M.K., Piet D.L. (2004). Molecular weight distribution in
is required given the output currents of the process and
low-density polyethylene polymerization; impact of scission
mechanisms in the case of a tubular reactor. Chemical Engineering
especially those that are gases.
Science, 59, 10: 2039-2052.
Ecopetrol. (2014). Quiénes somos. Disponible en: http://www.
quienes-somos/acerca-de-ecopetrol/. [Visitada en octubre de 2015].
EPA. (2011). Environmental Optimization Using the WAste Reduction
Through the simulation of processes that lack the
Algorithm (WAR). Disponible en: http://nepis.epa.gov/Exe/ZyPDF.
recycle of ethylene, it was concluded that the amount
cgi/P100DZKT.PDF?Dockey=P100DZKT.PDF. [Visitada en octubre
of ethylene that does not react is considerable, which
affects largely the efficiency of the process, reaching Idarraga L.M. (2010). Características de los reactores flujo piston.
only a 30 %. It should be recycled before a purification
caracteristicas-de-los-reactores-flujo.html. [Visitada en octubre
stage in order to increase the rate of the operative
profitability of the production process of LDPE.
Lipatov Y., Nesterov A. (1998). Polymer thermodynamic library.
Springer: Netherlands. 450 p.
Kienle A., Boll M., Schmith C.U., Schwibach M. (2005). Dynamic
simulation of a tubular reactor for the production of low-
density polyethylene using adaptive method of lines. Journal of
APCA. (2013). Nuestra alcaldía, ¿Quiénes somos? Alcaldía de
Computational and Applied Mathematics, 183: 288-300.
Puerto Colombia-Atlántico (APCA). Disponible en: http://www.
Malppas D.B. (2012). Introduction to Industrial Polypropylene:
Properties, Catalysts Processes. John Wiley & Sons: New York. 360 p.
en octubre de 2015].
Odian G. (2004). Principles of Polymerization. John Wiley & Sons:
Brandup J., Immergut E.H. (1989). Polymer Handbook. John Wiley:
New York. 812 p.
New York. 1850 p.
Rozzi N.L., Singh R.K. (2006). Supercritical fluids and food industry.
C&EN. (2014). C&EN's Global Top 50 Chemical Firms For 2014. Chemical
Comprehensive Reviews in Food Science and Food Safety, 1: 33-44.
& Engineering News (C&EN). Disponible en: http://cen.acs.org/
Textos Científicos. (2005). Obtención de Polietileno, Polietileno de
articles/92/i30/CENs-Global-Top-50-Chemical.html. [Visitada en
alta presión. Disponible en: http://www.textoscientificos.com/
octubre de 2015].
polimeros/polietileno/obtencion. [Visitada en octubre de 2015.
Cuevas R. (2012). Ingeniería de reactores. Disponible en: http://depa.
[Visitada en octubre de 2015].
Source: http://vector.ucaldas.edu.co/downloads/Vector10_9.pdf
Managing Ringworm in the Sport of Judo Report from Sports Medicine and Science Committee Introduction Due to the close contact inherent in the sport of judo, athletes are more susceptible to skin disorder transmissions. Many types of skin disorders exist and we will not be able to cover them all in this report. The focus will be on one particular skin condition affecting many judo athletes over the past 3 years… "Ringworm".
2015 ADEA ABSTRACT SUBMISSION PREPARATION Oral presentations and E-Poster presentations Selecting Your Program Streams The Program Organising Committee (POC) accepts submissions of abstracts of original contributions on any topic related to the following program streams: 1. Scientific 2. Program Evaluation/Review of Resource Delivery/Quality Improvement Activity 3. Clinical Practice/Case Studies/Service Delivery