Cavellaneda.com.ar
Trabajos Publicados
AN EXPANSIVE DOLOSTONE FROM ARGENTINA - THE COMMON
DILEMMA: ACR OR ANOTHER VARIANT OF ASR?
Carlos A. Milanesi 1*, Silvina Marfil 2,3, Pedro J. Maiza 2,4, Oscar R. Batic 5
1 Cementos Avellaneda S. A., Ciudad Autónoma de Buenos Aires, Buenos Aires, Argentina
2 Dpto. de Geología, Universidad Nacional del Sur - INGEOSUR, Bahía Blanca, Buenos Aires, Argentina
3 Comisión de Investigaciones Científicas (CIC), Buenos Aires, Argentina
4 Consejo Nacional de Investigaciones Científicas y Técnicas (CONICET), Buenos Aires, Argentina
5 LEMIT, Comisión de Investigaciones Científicas (CIC), La Plata, Buenos Aires, Argentina
Keywords: alkali-carbonate reaction, dedolomitization, mineral admixture, lithium
Abstract
Alkali-carbonate reaction is a known harmful reaction that affects concrete durability and constitutes
an issue of much controversy between researchers and concrete technologists. Since 1991, the authors have been working in this field to evaluate the possibility of the occurrence of this reaction in Argentina. The studies have shown the existence of a fine-grained dolostone that reacts deleteriously with concrete alkalis following a mechanism similar to ACR. This dolostone has two distinctive characteristics. First of all, the rock shows a clear dedolomitization reaction producing calcite and brucite (no siliceous gel was observed in thin sections). Secondly, the use of known mineral admixtures (fly ash, silica fume, ground granulated blast-furnace slag, natural pozzolan) or lithium compounds does not mitigate concrete expansion. This paper summarizes the results obtained with this dolomitic rock using current characterization techniques (ASTM C 586, ASTM C 227, NBRI, concrete prism expansion test, and polarization microscopy).
Concrete structures affected by alkali-carbonate reaction (ACR) have only been reported in Canada,
USA and China [1-4] and possibly in Austria [5]. In spite of that, this reaction has many distinctive characteristics which are very interesting for concrete technologists, not only from an academic point of view but also from engineering practice.
One of the most critical features of ACR is that concrete expansion cannot be effectively controlled
by combining either low or high alkali cement with mineral admixtures [6-10] or by using lithium-based chemical compounds [1,6,11,12].
An additional typical attribute of ACR is that the relationship between concrete or mortar expansion
and the grading of reactive aggregate is not like the one observed in alkali-silica reaction (ASR) [13]. This is the reason why there are some test methods especially designed to study ACR [5,14].
* Correspondence to:
[email protected]
Another common characteristic of concrete affected by ACR is that classical siliceous gel from ASR is
usually not detected or, at least, the correspondence between its quantity and concrete damage is not so obvious [1,7].
All the issues described above have been studied by many researchers all over the world [15-19] and all
of them are still subject of much controversy and an ongoing debate [20-22].
Although a number of concrete structures in Argentina have been deteriorated by ASR [23-26], there
is no one affected by ACR so far. The authors have been working in this field since 1991, to evaluate the possibility of the occurrence of this reaction with dolomitic rocks from Argentina [27,28].
The studies have shown the existence of a fine-grained dolostone that reacts deleteriously with
concrete alkalis following a mechanism similar to ACR [29,30]. This dolostone has two distinctive characteristics. First of all, the rock, used as coarse aggregate in concrete, shows a clear dedolomitization reaction producing calcite and brucite (siliceous gel was rarely observed in thin sections) [29]. Secondly, the use of efficient mineral admixtures (fly ash, silica fume, ground granulated blast-furnace slag, natural pozzolan) or lithium compounds for replacements frequently used for controlling ASR, does not inhibit concrete expansion [31].
This paper summarizes the results obtained with this dolomitic rock using current characterization
techniques (ASTM C 586, ASTM C 227, NBRI, concrete prism expansion test and polarization microscopy).
2 MATERIALS
2.1 Materials
Portland ceme nts
Ordinary Portland cements (type I according to ASTM C 150), with high (1.15 ± 0.01 % Na2Oeq) and
low (0.34 % Na2Oeq) alkali content (HAC and LAC, respectively), were used to make mortar and concrete
specimens.
Valcheta Dolostone (VD)
The rock studied is a dolostone from hydrothermal origin (Lower Tertiary), from Valcheta (Province
of Río Negro, Argentine). It is a porous rock, without alteration, composed by dolomite with minor amount
of quartz, feldspar and fragments of rhyolitic volcanic rocks. The grain size ranges from 10 to 30 μm. The
insoluble residue varies between 10 and 20 %. By XRD, illite, smectite and sepiolite were also identified in its
composition. Three different samples of this rock (a, b and c) were used throughout these studies.
Fine aggregate
Non-reactive siliceous sand was used. This sand, consisting of fresh and unaltered quartz and feldspar
grains, is a material of proved characteristics and widely used for preparing control mixes in testing research.
Mineral admixtures (MA)
Table 1 shows the type, origin and the main characteristics of the MA used in this study for preparing
mortar and concrete mixtures. The replacement percentages used of each MA were as follows: 30 wt%, for
natural pozzolan; 40 wt%, for fly ash; 60 wt%, for granulated blast-furnace slag; and 10 wt%, for silica fume.
2.2 Methods
Several alkali reactivity test methods were applied on rock, mortar and concrete specimens in order to
evaluate the ACR of the rock sample under study. The main guidelines of these test methods are given below.
Chemical method
A rock sample is analyzed for CaO/MgO ratio and Al2O3, according to CSA A23.2-26A [32]. The
results are plotted on a graph showing zones that correspond to aggregates potentially expansive or not, due to ACR [33].
Rock cylinder method
A modified version of ASTM C 586 [34] was applied for this study. Length changes were measured on
rock cylinders (19 mm in diameter and 75 mm in length) while immersed in 1N NaOH solution at 23 °C. The volume of alkali solution to the volume of rock specimen ratio was about 7.
Mortar bar test method (MBT)
25 x 25 x 285 mm mortar bars were made with HAC, according to ASTM C 227-87 [35] (i.e.
maintaining mortar flow between 100 and 110 and storing the bars in wicked containers). Mortar bar expansions were measured up to 12 months. MBT was both applied to evaluate the expansion behavior of VD and the effectiveness of the addition of 1.0 % LiCl (by weight of cement) to control the deleterious reaction. Some additional tests were conducted using the aggregate with a coarser grading. Mortar bar expansions greater than 0.05 % at 3 months or 0.10 % at 6 months are considered potentially deleterious.
Accelerated mortar bar test method (AMBT)
25 x 25 x 285 mm mortar bars were made with HAC, according to ASTM C9-P214 (similar to ASTM
C 1260), widely known as NBRI [36]. Mortar bar expansions were measured up to 28 days, maintaining the bars immersed in 1N NaOH solution at 80 °C. AMBT was both run to evaluate the expansion response of VD and the effectiveness of MA for inhibiting the expansive reaction.
Concrete prism test method (CPT)
75 x 75 x 360 mm concrete prisms were made using VD as coarse aggregate (19 mm-maximum size)
and non-reactive siliceous sand. Control concrete mixtures were prepared with the following characteristics: cement content of 310 kg/m3, HAC with an alkali content raised to 1.25 wt% of Na2Oeq (3.88 kg Na2Oeq/m3of concrete), coarse-to-fine aggregates ratio of 50:50 and a water-to-cement ratio (w/c) of 0.57. The prisms were put into sealed plastic bags, containing 100 ml of water (after Rogers and Hooton [37]), and stored at 38 °C. Concrete expansions were monitored up to 3 years. CPT was both used to evaluate the expansivity of VD and the effectiveness of MA for controlling the expansive reaction. A pair of concrete mixtures, with a smaller maximum size of coarse aggregate (10 mm), was also prepared to evaluate the inhibition effectiveness of lithium carbonate (Li2CO3). The dose used for this chemical addition was 2.8 % by weight of cement.
3 RESULTS
The results of the chemical analysis of VD are given in Table 1. Figure 1 shows a plot of CaO/MgO
ratio versus Al2O3. On the basis of these data, the rock under study would be considered innocuous.
Figure 2 shows a plot of expansion of rock cylinders immersed in 1N NaOH solution up to 1 year. In
this case, rock specimens (a-1, a-2 and a-3) were drilled form different pieces of rock randomly selected (bedding was not discernible). As this figure shows, expansive tendencies of rock specimens are evident after 28 days of immersion in alkali, being the cylinders expansion very different between them and well in excess of 0.1 %. Although a large number of cracks were observed on rock cylinders, no typical signs of ASR, such as gel or stains could be seen. Previous studies [29,30], performed by XRD and SEM analyses, found that a strong dedolomitization occurs near the surfaces of rock cylinders and calcite and brucite are clearly detected.
Table 3 shows the record of expansion of the MBT specimens at 3, 6 and 12 months. First of all,
these results show again, that VD has a clear expansion behavior resulting from the alkali attack. Comparing the results of the mixtures 2 and 3, it is also clear that the addition of 1 % LiCl has no effect at all on mortar expansion. Despite the expansion results of mortar mixtures 1 and 2 are not totally comparable (as they were prepared with different aggregate fractions), it appears to be that the use of a coarser grading promotes an increase of the expansion level of mortar bars, as is usually the case for the ACR [13,14]. Petrographic examination of the MBT specimens revealed unmistakable evidence of ACR (Figure 7). Indeed, calcitic reaction rims and cracks were clearly observed although no siliceous gel could be detected.
The expansion results of the AMBT at 16 and 28 days are given in Table 4. Although the expansive
tendency of VD is also detected by this test method, the expansion of mortar bars made from the control mixes (# 1, 2, 4, 5), according to ASTM C9-P214, is close to 0.10 % at 16 days. As it was observed in the MBT, when the mortar bars of the AMBT were made with a coarser aggregate fraction (1.2-4.8 mm), the expansion level was greater than that obtained in the mortar made with the whole grading of the aggregate (0.15-4.8 mm). It is also remarkable that, at later ages, mortar bars made with MA expanded more than the control (only HAC). Again, these results showed that none of the MA selected for this study (at replacements levels considered to be adequate for inhibiting the expansion of ASR, at least) was suitable for controlling the deleterious reaction caused by Valcheta dolostone.
Expansion curves of concretes made by either LAC or a combination of HAC and a mineral
admixture (MA) are shown in Figures 4 and 5. It should be noted that all the concretes tested appear to be still expanding at the end of the 3-year test period. In the same way, none of the MA selected for this study was suitable for controlling the deleterious reaction caused by VD (sample c). The use of concrete mixture
with low alkali content (≈ 1.0 kg Na2Oeq/m3) was not effective either (Figure 4). Concrete expansion was only
just reduced by 30 % using lithium carbonate (Figure 6).
4
DISCUSSION
It is clear from the above results that the dolomitic rock under study (VD) exhibits a clear expansive
behavior as a result of the alkali attack, although this rock does not reveal the characteristic texture and mineral composition typical of the alkali-carbonate reactive rocks [2,3,6,13].
From a petrographic point of view, VD has many interesting features. Firstly, it has fine-grained
dolomite crystals (< 50 µm) and a pore structure allowing alkali solution to penetrate the rock. Both conditions are considered very important for the reactivity of every dolomitic rock [3]. Secondly, contrary to the well know Canadian and American alkali-carbonate reactive rocks, VD has no calcite. This fact makes the rock to have a bulk composition very different to the known reactive carbonate aggregates and this could explain why the quick chemical screening test did not identify its deleterious alkali reactivity.
The rock has also a high insoluble residue with various siliceous components that might also promote
expansion due to ASR, considering the new approach emerged from the literature [21,22]. However, although reaction rims and cracks were clearly observed in mortar and concrete specimens, no siliceous gel could be identified by visual inspection or microscopical examination (as is usually the case in ACR). Only calcite and brucite were detected as a result of the dedolomitization reaction. Finally, while the presence of smectite makes the evaluation of this rock quite complicated, previous studies [29] have shown that this argillaceous component does not play any role in the expansion of the rock.
In agreement with the literature [1,8,14], MBT and AMBT were not effective in detecting the alkali-
reactivity of VD, since 1-year or 16-day mortar bar expansions, respectively, were less than 0.10 %. It is also clear that the use of an aggregate with a coarser grading induce an increase of the expansion level of mortar bars, as is usually the case for the ACR [13,14].
Above all, the most interesting feature of this study is that mortar or concrete expansion could not be
effectively controlled by combining either low or high alkali cement with mineral admixtures or by using
lithium-based chemical compounds, as it occurs in the case of ACR [1,8-12]. It is particularly remarkable that
using a concrete mixture with an alkali content as low as 1.0 kg Na2Oeq/m3 was not effective either. As it was
reported by Pagano and Cady [12], the use of lithium carbonate was not useful as a preventive measure.
5
CONCLUSIONS
study, the following conclusions can be drawn:
The dolostone under study reacts deleteriously with concrete alkalis following a mechanism similar to
ACR, despite the rock does not have the characteristic texture of the alkali-carbonate reactive rocks.
Based on the current knowledge, it is not possible to deny that ASR may take a part in the expansive
reaction, considering the potentially reactive components of the insoluble residue of the rock, although no siliceous gel could be detected.
ASR should be playing a role in the expansion mechanism of Valcheta dolostone, but it is not easy to
understand why the use of mineral admixtures and lithium-based compounds does not inhibit mortar and concrete expansion. It is also difficult to explain why the use of a concrete mixture with an alkali content as low as 1.0 kg Na2Oeq/m3 was not effective either.
The quick chemical screening test did not identify the deleterious alkali reactivity of Valcheta
dolostone as a result of its particular bulk composition.
MBT (ASTM C 227) and AMBT (ASTM C 1260) give both a wrong indication of the alkali
expansivity of the aggregate.
CPT proved to be the best method for evaluating the alkali reactivity of this rock.
REFERENCES
Swenson, EG (1957): A Reactive Aggregate Undetected by ASTM Tests. ASTM Bulletin (226): 48-51
[2] Grattan-Bellew,
J (1897): Three Decades of Studying the Alkali Reactivity of Canadian
Aggregates. In: Scanlon, JM (editor): Concrete Durability, Katharine and Bryan Mather International Conference, ACI SP 100, Vol. 2, Atlanta, Georgia (USA): 1365-1384
[3] Ozol, MA (2006): Alkali-Carbonate Reaction. In: Lamond, JF, and Pielert, JH (editors): Significance of
Tests and Properties of Concrete and Concrete-Making Materials, STP 169D, American Society for Testing Materials (ASTM), Philadelphia (USA), Chapter 35: 410-424
Deng, M, Han, SF, Lu, YN, Lan, XH, Hu, YL, and Tang, MS (1993): Deterioration of Concrete Structures due to Alkali-Dolomite Reaction in China. Cement & Concrete Research (23): 1040-1046
Sommer, H, Grattan-Bellew P, Katayama, T, and Tang, M (2004): Development and Inter-Laboratory Trial of the RILEM AAR-5 Rapid Preliminary Screening Test for Carbonate Aggregates. In: Tang, M, & Deng, M (editors): Proceedings of the 12th International Conference on Alkali-Aggregate Reaction in Concrete, Beijing (China) (1): 407-412
Alkali-Carbonate Rock Reaction. In: Proceedings of the
Symposium on Alkali-Carbonate Rock Reactions, Highway Research Record, H. R. T. B., Washington, DC (45): 21-40
Williams, DA, and Rogers, CA (1991): Field Trip Guide to Alkali Carbonate Reactions in Kingston, Ontario. Report MI 145, Ministry of Transportation of Ontario, Engineering Materials Office: pp26
Thomas, MDA, and Innis, FA (1998): Effect of Slag on Expansion Due to Alkali-Aggregate Reaction in Concrete. ACI Materials Journal (95/6): 716:724
Rogers, CA, and Hooton, RD (1992): Comparison between Laboratory and Field Expansion of Alkali-Carbonate Reactive Concrete. In: Poole, AB (editor): Proceedings of the 9th International Conference on Alkali-Aggregate Reaction in Concrete, London (UK) (2): 877-884
[10] Deng, M, and Tang, MS (1993): Measures to Inhibit Alkali-Dolomite Reaction. Cement & Concrete
Research (23): 1115-1120
[11] Hudec, PP, and Larbi, JA (1989): Chemical Treatment and Additives to Minimize Alkali Reactivity. In:
Okada, K, Nishibayashi, S, & Kawamura, M (editors): Proceedings of the 8th International Conference on Alkali-Aggregate Reaction in Concrete, Kyoto (Japan): 193-198
[12] Pagano, MA, and Cady, PD (1982): A Chemical Approach to the Problem of Alkali-Reactive
Carbonate Aggregates. Cement & Concrete Research (12): 1-12
Reactivity of Dolomitic Carbonate Rocks. In: Proceedings of the
Symposium on Alkali-Carbonate Rock Reactions, Highway Research Record, H. R. T. B., Washington, DC (45): 1-20.
[14] Lu, D, Fournier, B, Grattan-Bellew, PE, Xu, Z, and Tang, M (2008): Development of a Universal
Accelerated Test for Alkali-Silica and Alkali-Carbonate Reactivity of Concrete Aggregates. Materials & Structures (41): 235-246
[15] López-Buendía, AM, Climent, V, Mar Urquiola, M, and Bastida, J (2008): Influence of Dolomite
Stability on Alkali-Carbonate Reaction. In: Broekmans MATM & Wigum BJ (editors), Proceedings of the 13th International Conference on Alkali-Aggregate Reaction in Concrete, Trondheim (Norway): pp10
P Silveira, ALZ, Hasparyk, NP, Chiossi, WC, Dos Anjos Farias, L, and Rahal Lenharo, SL (2008): Investigation of Alkali-Aggregate Reaction in Brazilian Carbonate Rocks. In: Broekmans MATM & Wigum BJ (editors), Proceedings of the 13th International Conference on Alkali-Aggregate Reaction in Concrete, Trondheim (Norway): pp12
[17] Samuel, G, Wason, RC, and Mullick, AK (1989): Evaluation of AAR Potential of Limestone
Aggregates in India. In: Okada, K, Nishibayashi, S, & Kawamura, M (editors): Proceedings of the 8th International Conference on Alkali-Aggregate Reaction in Concrete, Kyoto (Japan): 235-240
[18] Poole, AB (1981): Alkali-Carbonate Reactions in Concrete. In: Proceedings of the 5th International
Conference on Alkali-Aggregate Reaction in Concrete, Cape Town (South Africa), National Building Research Institute (NBRI), Paper S252/34: pp9
[19] Sims, I, and Sotiropoulos, P (1983): Standard Alkali Reactivity Testing of Carbonate Rocks from the
Middle East and North Africa. In: Proceedings of the 6th International Conference on Alkalies in Concrete, Danish Concrete Institute, Copenhagen (Denmark): 337-349
[20] Tang, M, Deng, M, Lan, X, and Han, S (1994): Studies on Alkali-Carbonate Reaction. ACI Materials
Journal (91/1): 26-29
[21] Grattan-Bellew, PE, Margeson, J, Mitchell, LD, and Min, D (2008): Is ACR Just another Variant of
ASR? - Comparison of Acid Insoluble Residues of Alkali-Silica and Alkali-Carbonate Reactive Limestones and Its Significance for the ASR/ACR Debate. In: Broekmans MATM & Wigum BJ (editors), Proceedings of the 13th International Conference on Alkali-Aggregate Reaction in Concrete, Trondheim (Norway): pp11
Katayama, T (2004): How to Identify Carbonate Rock Reactions in Concrete. Materials
Characterization (53): 85-104
[23] Giovambattista, A, Batic, OR, and Traversa, LP (1986): Reactivity of Alkalis and Sandstone Cemented
with Opal and Chalcedony. In: P. E. Grattan Bellew (editor), Proceedings of the 7th International Conference on Alkali-Aggregate Reaction in Concrete, Ottawa (Canada), Noyes Publication: 408-412
[24] Marfil, SA, and Maiza, PJ (2008): Petrographic Study of a Building Deteriorated Due to Alkali-Silica
Reaction. In: Broekmans MATM & Wigum BJ (editors), Proceedings of the 13th International Conference on Alkali-Aggregate Reaction in Concrete, Trondheim (Norway): pp8
[25] Milanesi, CA, Souza, E, Marfil, SA, and Maiza, PJ (2008): Estudio de las manifestaciones de RAS
detectadas en el pavimento de hormigón de la Ruta Nacional Nº 127 y su relación con el deterioro de la obra. In: Rahhal, V, & Sota, JD (editors): Proceedings of the 3rd International Congress of the Argentinean Association of Concrete Technology (AATH), Córdoba (Argentina): 273-280
[26] Batic, OR, Sota, JD, and Serrani, HR (1984): Estudio de las posibles causas de deterioro del hormigón
de la pista de aterrizaje y zona de servicio del aeropuerto de Camba Punta – Corrientes. In: Asociación Argentina de Tecnología del Hormigón (editor): Proceedings of the 6th Technical Meeting of AATH, Olavarría (Argentina), (2): 249-270
[27] Batic, OR, Cortelezzi, C, Maiza, PJ, Marfil, SA, Milanesi, CA, and Pavlicevic, R (1991): Reacción
deletérea de algunas rocas dolomíticas en hormigones. In: Asociación Argentina de Tecnología del Hormigón (editor): Proceedings of the 10th Technical Meeting "Ing. Juan F. García Balado", Olavarría (Argentina) (2): 95-113
[28] Batic, OR, and Milanesi, CA (1991): Experiencias sobre la reacción álcali-carbonato con rocas
dolomíticas. Revista Hormigón (19): 15-29
[29] Milanesi, CA, and Batic, OR (1994): Alkali Reactivity of Dolomitic Rocks from Argentina. Cement &
Concrete Research (24/6): 1073-1084
[30] Milanesi, CA, Marfil, S, Batic, OR, and Maiza, PJ (1996): The Alkali-Carbonate Reaction and its
Reaction Products. An Experience with Argentinean Dolomite Rocks. Cement & Concrete Research (26/10): 1579-1591
Comportamiento de algunas adiciones minerales activas frente a la
reacción álcali-carbonato. Revista Hormigón (23): 41-51
[32] A23.2-26A (2009): Determination of Potential Alkali-Carbonate Reactivity of Quarried Carbonate
Rocks by Chemical Composition. Test Methods and Standard Practices for Concrete, Canadian Standards Association, Mississauga, Ontario (Canada): 366-370
[33] Rogers, CA (1986): Evaluation of the Potential for Expansion and Cracking of Concrete Caused by
the Alkali-Carbonate Reaction. Cement, Concrete, & Aggregates, CCAGDP (8/1): 13-23
[34] ASTM C 586-86 (1991): Standard Test Method for Potential Alkali Reactivity of Carbonate Rock for
Concrete Aggregate (Rock Cylinder Method). Annual Book of ASTM Standards, (04.02) Concrete and Mineral Aggregates, American Society for Testing and Materials, Philadelphia, PA, USA: 287-290
[35] ASTM C 227-87 (1991): Standard Test Method for Potential Alkali Reactivity of Cement-Aggregate
Combinations (Mortar Bar Method), Annual Book of ASTM Standards (04.02) Concrete and Mineral Aggregates, American Society for Testing and Materials, Philadelphia, PA, USA: 157-162
ASTM C 9-P214 (1991): Proposed Test Method for Accelerated Detection of Potentially Deleterious Expansion of Mortar Bars Due to Alkali-Silica Reaction. Annual Book of ASTM Standards, (04.02) Concrete and Mineral Aggregates, American Society for Testing and Materials, Philadelphia, PA, USA: 755-758
[37] Rogers, CA, and Hooton, RD (1989): Leaching of Alkalis in Alkali-Aggregate Reaction Testing. In:
Okada, K, Nishibayashi, S, & Kawamura, M (editors): Proceedings of the 8th International Conference on Alkali-Aggregate Reaction in Concrete, Kyoto (Japan): 327-332
TABLE 1. Chemical composition of Valcheta dolostone (VD)
TABLE 2. Mineral admixtures
ArgentinaMendoza,
Fly ash (class F according to
Granulated blast-furnace slag
na: Not available
TABLE 3. Expansion of mortar bars at 38°C (MBT)
Mortar bar expansion (%) at:
TABLE 4. Expansion of mortar bars in 1N NaOH solution at 80°C (AMBT)
Expansion (%) of mortar bar at:
Control Test mix Control Test mix Test to control
(1) HAC (without mineral admixture); (2) HAC + mineral admixture
Aggregates considered non-
expansive due to ACR
Aggregates considered
potentially expansive due
Aggregates considered non-expansive due to ACR
Al2O3 (%)
FIGURE 1. Result of CSA A23.2-26A chemical test
rednil 1,0
yc kco 0,5
Cylinders: Ø = 19 mm, L = 70 mm
Solution: 1N NaOH at 23 °C
Time of immersion in 1N NaOH solution (months)
FIGURE 2. Expansion of rock cylinders in 1N NaOH solution
HACHAC + 30 % NPM
%( noi 0,15
s
napxe r 0,10
Time of immersion in 1N NaOH solution at 80°C (days)
FIGURE 3. Expansion of mortar bars using different MA (AMBT)
3,88 kg Na2Oeq/m3
1,05 kg Na2Oeq/m3
xe ete 0,08
Concrete prisms: 75 x 75 x 360 mm
Maximum size of coarse aggregate: 19 mm (3/4")
Time (years)
FIGURE 4. Expansion of concrete prisms (VD-c) using LAC or HAC + FA (CPT)
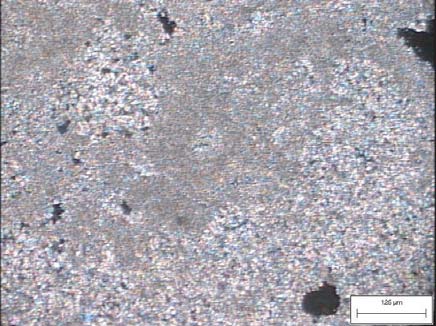
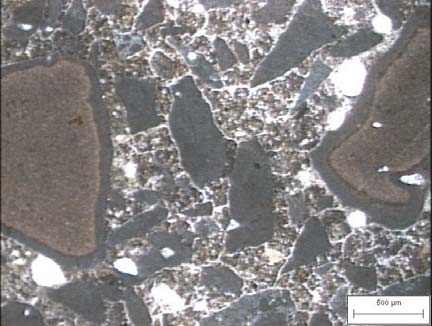
e ete 0,08
Concrete prisms: 75 x 75 x 360 mm
Maximum size of coarse aggregate: 19 mm (3/4")
Time (years)
FIGURE 5. Expansion of concrete prisms using different MA (CPT)
HACLithium carbonate
)
%( nois 0,12
a
pxe ete 0,08
Concrete prisms: 75 x 75 x 360 mm
Maximum size of coarse aggregate: 10 mm (3/8")
Time (years)
FIGURE 6. Expansion of concrete prisms using lithium carbonate (CPT)
b) mortar bar (MBT) at 5 years
FIGURE 7. Polarization microscopy of VD rock sample
Source: http://www.cavellaneda.com.ar/pdf_publicaciones/CA_ca_publicacion_007pdf_10.pdf
Case Study Dr. Tabitha Ndungu presented to NACADA on their 2nd Conference in Nairobi, Kenya Date; 10th - 14th JUNE 2013 Venue: Moi Sports Centre Kasarani Gymnasium Theme: " The Youth and Drugs: A Call to Action." In spite of the damage done by
Koka, Deane & Lambert Health Worker Confidence in Diagnosing and Treating Mental Health Problems Health worker confidence in diagnosing and treating mental health problems in Papua New Guinea Betty E. Koka, Frank P. Deane and Gordon Lambert Illawarra Institute for Mental Health University of Wollongong Abstract