Traits of a healthy safety culture
Document
INPO 12–012
April 2013
Traits of a
Healthy Nuclear
Safety Culture
Revision 1
OPEN DISTRIBUTION
OPEN DISTRIBUTION: Copyright 2012, 2013 by the Institute of Nuclear Power Operations. Not for sale or commercial use. All
other rights reserved.
NOTICE: This information was prepared in connection with work sponsored by the Institute of Nuclear Power Operations (INPO).
Neither INPO, INPO members, INPO participants, nor any person acting on behalf of them (a) makes any warranty or
representation, expressed or implied, with respect to the accuracy, completeness, or usefulness of the information contained in this
document, or that the use of any information, apparatus, method, or process disclosed in this document may not infringe on privately
owned rights, or (b) assumes any liabilities with respect to the use of, or for damages resulting from the use of any information,
apparatus, method, or process disclosed in this document.
INPO 12-012, Revision 1
TABLE OF CONTENTS
INPO 12-012, Revision 1
This page is intentionally blank.
INPO 12-012, Revision 1
Traits of a Healthy Nuclear Safety Culture builds on the knowledge and experience gained since the publication of
Principles of a Strong Nuclear Safety Culture in 2004. The change in the title reflects the commercial nuclear industry alignment of its own terminology with that used by the U.S. Nuclear Regulatory Commission. This document was developed through a collaborative effort by U.S. industry personnel and the staff of the Institute of Nuclear Power Operations (INPO), with input from representatives of various regulatory agencies, the public, and the nuclear industry worldwide.
Traits of a Healthy Nuclear Safety Culture reflects an alignment in two sets of terms that have been used to describe nuclear safety culture: INPO and the industry defined safety culture in leadership terms of principles and attributes, and the U.S. Nuclear Regulatory Commission defined safety culture in regulatory terms of components and aspects. Whereas each set of terms served its special function, the result created confusion within operating organizations as to the essential elements of a healthy safety culture.
Traits of a Healthy Nuclear Safety Culture describes the essential traits and attributes of a healthy nuclear safety culture, with the goal of creating a framework for open discussion and continuing evolution of safety culture throughout the commercial nuclear energy industry. For the purposes of this document, a trait is defined as a pattern of thinking, feeling, and behaving such that safety is emphasized over competing priorities. Experience has shown that the personal and organizational traits described in this document are present in a positive safety culture and that shortfalls in these traits and attributes contribute significantly to plant events. Rather than prescribing a specific program or implementation method, this document describes the basic traits. These traits and attributes, when embraced, will be reflected in the values, assumptions, behaviors, beliefs, and norms of an organization and its members. Ideally, the traits will describe what it is like to work at a nuclear facility and how things are done there. Traits appear in boldface. The attributes clarify the intent of the traits. Every nuclear organization has many important behaviors and actions specified within its procedures, processes, written standards, and expectations. This document highlights some of these behaviors and actions that are most critical to creating and maintaining a healthy nuclear safety culture. The behaviors and actions contained herein are representative and should not be considered comprehensive; as such, this document is not intended to be used as a checklist. It is encouraged that this document be considered for inclusion and use in self-assessments, root cause analyses, and training content, as appropriate. Utility managers are encouraged to make in-depth comparisons between these traits and their day-to-day policies and practices and to use any differences as a basis for improvements. In addition to the traits and attributes, two addendums are available.
Addendum I: Behaviors and Actions That Support a Healthy Nuclear Safety Culture by Organizational Level describes nuclear safety behaviors and actions that contribute to a healthy nuclear safety culture by organizational level―executive/senior manager, manager, supervisor,
INPO 12-012, Revision 1
and individual contributor. Supplemental workers are included in the individual contributor level.
Addendum II: Cross-References provides cross-references from INPO 12-012,
Traits of a Healthy Nuclear Safety Culture, to the previous
Principles of a Strong Nuclear Safety Culture, the U.S. Nuclear Regulatory Commission operating reactor assessment program cross-cutting area components, and the International Atomic Energy Agency safety culture characteristics. This cross-reference can help individuals understand how the framework was developed and can be useful in change management efforts in this important area.
INPO 12-012, Revision 1
BACKGROUND
Watershed events over the years have influenced the safety culture at U.S. commercial nuclear power plants. The industry had its first significant wake-up call in 1979 as a result of the accident at Three Mile Island Nuclear Station. Many fundamental problems involving hardware, procedures, training, and attitudes toward safety and regulation contributed to the event. In 1986, the Chernobyl Nuclear Power Plant accident in the Ukraine was a stark reminder of the hazards of nuclear technology. This accident resulted from many of the same weaknesses that had led to the Three Mile Island accident. In addition, it highlighted the importance of maintaining design configuration, plant status control, line authority for reactor safety, and cultural attributes related to safety. Response from industry and regulatory organizations to both these events was sweeping. Improvements were made in standards, hardware, emergency procedures, processes, training (including simulators), emergency preparedness, design and configuration control, testing, human performance, and attitudes toward safety. The 2002 discovery of degradation of the Davis-Besse Nuclear Power Station reactor vessel head highlighted problems that develop when the safety environment at a plant receives insufficient attention. Most recently, the 2011 nuclear accident at the Fukushima Daiichi power plant in Japan illustrates the importance of thoroughly assessing possible nuclear safety impacts of a hypothetical, yet credible, extreme external event. It also highlights the importance of emergency response command and control, training, and resource availability for such an event. A theme common in these events is that, over time, problems crept in, often related to or a direct result of the plant culture. Had these problems been recognized, challenged, and resolved, the events could have been prevented or their severity lessened. The series of decisions and actions that resulted in these events can usually be traced to the shared assumptions, values, and beliefs of the organization. These events and the notion that culture is a key ingredient in the overall success of the plant form the basis for this document. Organizational culture is the shared basic assumptions that are developed in an organization as it learns and copes with problems. The basic assumptions that have worked well enough to be considered valid are taught to new members of the organization as the correct way to perceive, think, act, and feel. Culture is the sum total of a group's learning.
Culture is for the group what character and personality are for the individual.
INPO 12-012, Revision 1
In addition to a healthy organizational culture, each nuclear station, because of the special
characteristics and unique hazards of the technology—radioactive byproducts,
concentration of energy in the reactor core, and decay heat—needs a healthy
safety
culture. Nuclear safety culture is defined as the core values and behaviors resulting from a
collective commitment by leaders and individuals to emphasize safety over
competing goals to ensure protection of people and the environment.
This updated definition was developed to apply broadly across all industries that use
nuclear technologies. For the commercial nuclear power industry, nuclear safety
remains the overriding priority. Although the same traits apply to radiological safety,
industrial safety, security, and environmental safety, nuclear safety is the first value
adopted at a nuclear station and is never abandoned.
Nuclear safety is a collective responsibility. The concept of nuclear safety culture applies
to every employee in the nuclear organization, from the board of directors to the
individual contributor. No one in the organization is exempt from the obligation to
ensure safety first.
The performance of individuals and organizations can be monitored and trended and,
therefore, may serve as an indicator of the health of an organization's safety culture.
However, the health of a facility's safety culture could lie anywhere along a broad
continuum, depending on the degree to which the attributes of safety culture are
embraced. Even though safety culture is somewhat of an intangible concept, it is possible
to determine whether a station tends toward one end of the continuum or the other.
Commercial nuclear power plants are designed, built, and operated to produce electricity.
Safety, production, and cost control are necessary goals for the operation of such a plant.
These outcomes are quite complementary, and most plants today achieve high levels of
safety, impressive production records, and competitive costs, reinforced by decisions and
actions made with a long-term view. This perspective keeps safety as the overriding
priority for each plant and for each individual associated with it.
Nuclear safety culture is a leadership responsibility. Experience has shown that leaders
in organizations with a healthy safety culture foster safety culture through activities such
as the following:
• Leaders reinforce safety culture at every opportunity. The health of safety
culture is not taken for granted.
• Leaders frequently measure the health of safety culture with a focus on trends
rather than absolute values.
• Leaders communicate what constitutes a healthy safety culture and ensure
everyone understands his or her role in its promotion.
INPO 12-012, Revision 1
• Leaders recognize that safety culture is not all or nothing but is, rather,
constantly moving along a continuum. As a result, there is a comfort in discussing safety culture within the organization as well as with outside groups, such as regulatory agencies.
The traits described in this document are divided into three categories that are similar to the three categories of safety culture in International Nuclear Safety Advisory Group (INSAG)-4,
Safety Culture. The categories and their primary traits are as follows:
• Individual Commitment to Safety
— Personal Accountability
— Questioning Attitude
— Effective Safety Communication
• Management Commitment to Safety
— Leadership Safety Values and Actions
— Decision-Making
— Respectful Work Environment
• Management Systems
— Continuous Learning
— Problem Identification and Resolution
— Environment for Raising Concerns
— Work Processes
INPO 12-012, Revision 1
This page is intentionally blank.
INPO 12-012, Revision 1
THE TRAITS AND THEIR ATTRIBUTES
Individual Commitment to Safety
Personal Accountability
All individuals take personal responsibility for safety. Responsibility and
authority for nuclear safety are well defined and clearly understood. Reporting
relationships, positional authority, and team responsibilities emphasize the
overriding importance of nuclear safety.
Attributes:
PA.1 Standards: Individuals understand the importance of adherence to
nuclear standards. All levels of the organization exercise accountability for shortfalls in meeting standards. Behavior Examples: a. Individuals encourage each other to adhere to high standards.
b. Individuals demonstrate a proper focus on nuclear safety and
reinforce this focus through peer coaching and discussions.
c. Individuals hold themselves personally accountable for modeling
nuclear safety behaviors.
d. Individuals across the organization apply nuclear safety standards
e. Individuals actively solicit and are open to feedback.
f. Individuals help supplemental personnel understand and practice
expected behaviors and actions.
PA.2 Job Ownership: Individuals understand and demonstrate personal
responsibility for the behaviors and work practices that support nuclear safety.
Behavior Examples: a. Individuals understand their personal responsibility to foster a
professional environment, encourage teamwork, and identify challenges to nuclear safety.
b. Individuals understand their personal responsibility to raise nuclear
safety issues, including those identified by others.
c. Individuals take ownership for the preparation and execution of
assigned work activities.
INPO 12-012, Revision 1
d. Individuals actively participate in prejob briefings, understanding
their responsibility to raise nuclear safety concerns before work begins.
e. Individuals ensure that they are trained and qualified to perform
f. Individuals understand the objective of the work activity, their role
in the activity, and their personal responsibility for safely accomplishing the overall objective.
PA.3 Teamwork: Individuals and work groups communicate and coordinate
their activities within and across organizational boundaries to ensure nuclear safety is maintained.
Behavior Examples: a. Individuals demonstrate a strong sense of collaboration and
cooperation in connection with projects and operational activities.
b. Individuals work as a team to provide peer-checks, verify
certifications and training, ensure detailed safety practices, actively peer coach new personnel, and share tools and publications.
c. Individuals strive to meet commitments.
Questioning Attitude
Individuals avoid complacency and continuously challenge existing
conditions and activities in order to identify discrepancies that might result
in error or inappropriate action. All employees are watchful for assumptions,
anomalies, values, conditions, or activities that can have an undesirable effect on
plant safety.
Attributes:
QA.1 Nuclear is Recognized as Special and Unique: Individuals understand
that complex technologies can fail in unpredictable ways. Behavior Examples: a. The organization ensures that activities that could affect reactivity
are conducted with particular care, caution, and oversight.
b. Individuals recognize the special characteristics and unique
hazards of nuclear technology, including radioactive byproducts, concentration of energy in the core, and decay heat.
INPO 12-012, Revision 1
c. Individuals recognize the particular importance of features
designed to maintain critical safety functions, such as core and spent fuel cooling.
d. Executives and senior managers ask probing questions to
understand the implications and consequences of anomalies in plant conditions.
e. Executives and senior managers challenge managers to ensure
degraded conditions are fully understood and appropriately resolved, especially those involving equipment important to nuclear safety.
QA.2 Challenge the Unknown: Individuals stop when faced with uncertain
conditions. Risks are evaluated and managed before proceeding. Behavior Examples: a. Leaders reinforce expectations that individuals take the time to do
the job right the first time, seek guidance when unsure, and stop if an unexpected condition or equipment response is encountered.
b. Individuals maintain a questioning attitude during prejob briefings
and job-site reviews to identify and resolve unexpected conditions.
c. Individuals challenge unanticipated test results rather than
rationalizing them. For example, abnormal indications are not automatically attributed to indication problems but are thoroughly investigated before activities are allowed to continue.
d. Individuals communicate unexpected plant responses and
conditions to the control room.
e. Individuals stop work activities when confronted with an
unexpected condition, communicate with supervisors, and resolve the condition prior to continuing work activities. When appropriate, individuals consult system and equipment experts.
f. If a procedure or work document is unclear or cannot be performed
as written, individuals stop work until the issue is resolved.
QA.3 Challenge Assumptions: Individuals challenge assumptions and offer
opposing views when they think something is not correct.
1 Job-site review: An action performed by an individual or group to improve situational awareness at the job site; also known
as two-minute drill,
timeout,
two-minute rule,
take-a-minute, and
two-minute timeout.
INPO 12-012, Revision 1
Behavior Examples: a. Leaders solicit challenges to assumptions when evaluating nuclear
b. Individual contributors ask questions to fully understand the bases
of operational and management decisions that appear to be contrary to nuclear safety.
c. Managers question assumptions, decisions, and justifications that
do not appear to consider impacts to nuclear safety sufficiently.
QA.4 Avoid Complacency: Individuals recognize and plan for the
possibility of mistakes, latent problems, and inherent risk, even while expecting successful outcomes.
Behavior Examples: a. The organization is aware that latent conditions can exist,
addresses them as they are discovered, and considers the extents of the conditions and their causes.
b. Prior to authorizing work, individuals verify procedure
prerequisites are met rather than assuming they are met based on general plant conditions.
c. Individual contributors perform a thorough review of the work site
and the planned activity every time work is performed rather than relying on past successes and assumed conditions.
d. Leaders ensure specific contingency actions are discussed and
understood during job planning and prejob briefings.
e. Individuals consider potential undesired consequences of their
actions prior to performing work and implement appropriate error reduction tools.
Effective Safety Communication
Communications maintain a focus on safety. Safety communication is broad
and includes plant-level communication, job-related communication, worker-level
communication, equipment labeling, operating experience, and documentation.
Leaders use formal and informal communication to convey the importance of
safety. The flow of information up the organization is considered to be as
important as the flow of information down the organization.
Attributes:
CO.1 Work Process Communications: Individuals incorporate safety
communications in work activities.
INPO 12-012, Revision 1
Behavior Examples: a. Communications within work groups are timely, frequent, and
b. Work groups and supervisors communicate work statuses with
other work groups and supervisors during the performance of their work activities.
c. Individuals communicate with each other such that everyone has
the information necessary to accomplish work activities safely and effectively.
d. Communications during shift turnovers and prejob briefings
provide information necessary to support nuclear safety.
e. Work groups integrate nuclear safety messages into daily activities
CO.2 Bases for Decisions: Leaders ensure that the bases for operational and
organizational decisions are communicated in a timely manner.
Behavior Examples: a. Leaders promptly communicate expected outcomes, potential
problems, planned contingencies, and abort criteria for important operational decisions.
b. Leaders share information on a wide range of issues with
individuals and periodically verify their understanding of the information.
c. Leaders take steps to avoid unintended or conflicting messages that
may be conveyed by operational decisions.
d. Leaders encourage individuals to ask questions if they do not
understand the basis of an operational or management decision.
e. Executives and senior managers communicate the reasons for
resource allocation decisions, including the nuclear safety implications of those decisions.
CO.3 Free Flow of Information: Individuals communicate openly and
candidly, both up, down, and across the organization and with oversight, audit, and regulatory organizations. Behavior Examples: a. Leaders encourage the free flow of information.
b. Individuals share information openly and candidly.
INPO 12-012, Revision 1
c. Leaders respond to individuals in an open, honest, and
nondefensive manner.
d. Individuals provide complete, accurate, and forthright information
to oversight, audit, and regulatory organizations.
e. Leaders actively solicit feedback, listen to concerns, and
communicate openly with all individuals.
f. Leaders candidly communicate the results of monitoring and
assessments throughout the organization and with independent oversight organizations.
CO.4 Expectations: Leaders frequently communicate and reinforce the
expectation that nuclear safety is the organization's overriding priority.
Behavior Examples: a. Executives and senior managers communicate expectations
regarding nuclear safety so that individuals understand that safety is the highest priority.
b. Executives and senior managers implement a strategy of frequent
communication using a variety of tools to reinforce that nuclear safety is the overriding priority.
c. Executives and senior managers reinforce the importance of
nuclear safety by clearly communicating its relationship to strategic issues, including budget, workforce planning, equipment reliability, and business plans.
d. Leaders communicate desired nuclear safety behaviors to
individuals, providing examples of how behaviors positively or negatively affect nuclear safety.
e. Leaders routinely verify that communications on the importance of
nuclear safety have been heard and understood.
f. Leaders ensure supplemental personnel understand expected
behaviors and actions necessary to maintain nuclear safety.
INPO 12-012, Revision 1
Management Commitment to Safety
Leadership Safety Values and Actions
Leaders demonstrate a commitment to safety in their decisions and
behaviors. Executive and senior managers are the leading advocates of nuclear
safety and demonstrate their commitment both in word and action. The nuclear
safety message is communicated frequently and consistently, occasionally as a
stand-alone theme. Leaders throughout the nuclear organization set an example
for safety. Corporate policies emphasize the overriding importance of nuclear
safety.
Attributes
LA.1 Resources: Leaders ensure that personnel, equipment, procedures, and
other resources are available and adequate to support nuclear safety. Behavior Examples: a. Managers ensure staffing levels are consistent with the demands
related to maintaining safety and reliability.
b. Managers ensure sufficient qualified personnel are available to
maintain work hours within working hour guidelines during all modes of operation.
c. Managers ensure facilities are available and are regularly
maintained, including physical improvements, simulator fidelity, and emergency facilities.
d. Leaders ensure tools, equipment, procedures, and other resource
materials are available to support successful work performance, including risk management tools and emergency equipment.
e. Executives and senior managers ensure sufficient corporate
resources are allocated to the nuclear organization for short- and long-term safe and reliable operation.
f. Executives and senior managers ensure a rigorous evaluation of the
nuclear safety implications of deferred work.
LA.2 Field Presence: Leaders are commonly seen in working areas of the
plant observing, coaching, and reinforcing standards and expectations. Deviations from standards and expectations are corrected promptly.
Behavior Examples: a. Senior managers ensure supervisory and management oversight of
work activities, including contractors and supplemental personnel, such that nuclear safety is supported.
INPO 12-012, Revision 1
b. Leaders from all levels in the organization are involved in
overseeing work activities.
c. Managers and supervisors practice visible leadership in the field
and during safety-significant evolutions by "placing eyes on the problem," coaching, mentoring, reinforcing standards, and reinforcing positive decision-making practices and behaviors.
d. Managers and supervisors discuss their observations in detail with
the group they observed and provide useful feedback about how to improve individual performance.
e. Managers encourage informal leaders to model safe behaviors and
high standards of accountability.
LA.3 Incentives, Sanctions, and Rewards: Leaders ensure incentives,
sanctions, and rewards are aligned with nuclear safety policies and reinforce behaviors and outcomes that reflect safety as the overriding priority.
Behavior Examples: a. Managers ensure disciplinary actions are appropriate, consistent,
and support both nuclear safety and a safety-conscious work environment.
b. Managers reward individuals who identify and raise issues that
affect nuclear safety.
c. Leaders foster an environment that promotes accountability and
hold individuals accountable for their actions.
d. Managers consider the potential chilling effects of disciplinary
actions and other potentially adverse personnel actions and take compensatory actions when appropriate.
e. Leaders publicly praise behaviors that reflect a positive safety
LA.4 Strategic Commitment to Safety: Leaders ensure plant priorities are
aligned to reflect nuclear safety as the overriding priority.
Behavior Examples: a. Executives and senior managers reinforce nuclear safety as the
overriding priority.
b. Managers develop and implement cost and schedule goals in a
manner that reinforces the importance of nuclear safety.
INPO 12-012, Revision 1
c. Managers ensure production requirements are established,
communicated, and put into practice in a manner that reinforces nuclear safety.
d. Executives and senior managers use information from independent
oversight organizations to establish priorities that align with nuclear safety.
e. Executives and senior managers establish strategic and business
plans that reflect the importance of nuclear safety over production.
f. Executives and senior managers ensure corporate priorities are
aligned with nuclear safety.
LA.5 Change Management: Leaders use a systematic process for evaluating
and implementing change so that nuclear safety remains the overriding priority. Behavior Examples: a. When making decisions related to major changes, managers use a
systematic process for planning, coordinating, and evaluating the safety impacts and potential negative effects on the willingness of individuals to raise safety concerns. This includes decisions concerning changes to organizational structure and functions, leadership, policies, programs, procedures, and resources.
b. Executives and senior managers ensure nuclear safety is
maintained when planning, communicating, and executing major changes.
c. Managers maintain a clear focus on nuclear safety when
implementing the change management process, to avoid significant unintended consequences.
d. Managers ensure that individuals understand the importance of,
and their role in, the change management process.
e. Managers anticipate, manage, and communicate the effects of
impending changes.
f. Managers and supervisors actively monitor and address potential
distractions from nuclear safety during periods of change.
LA.6 Roles, Responsibilities, and Authorities: Leaders clearly define roles,
responsibilities, and authorities to ensure nuclear safety. Behavior Examples: a. Leaders ensure roles, responsibilities, and authorities are clearly
defined, understood, and documented.
INPO 12-012, Revision 1
b. Managers appropriately delegate responsibility and authority to
promote ownership and accountability.
c. Executives and senior managers ensure both corporate managers
who support the nuclear organization and managers at the station understand their respective roles and responsibilities.
d. Recommendations and feedback from corporate governance,
review boards, and independent oversight organizations do not override senior managers' ultimate responsibility for decisions that affect nuclear safety.
LA.7 Constant Examination: Leaders ensure that nuclear safety is
constantly scrutinized through a variety of monitoring techniques, including assessments of nuclear safety culture. Behavior Examples: a. Executives and senior managers ensure that board members and
members of independent oversight organizations meet with leaders and individual contributors in their work environments to develop an understanding of the status of the organization's safety culture.
b. Executives and senior managers obtain outside perspectives of
nuclear safety through the selection of qualified, critical independent safety review board members with diverse backgrounds and perspectives.
c. Executives and senior managers use a variety of monitoring
tools—including employee surveys, independent and self-assessments, external safety review board member feedback, and employee concern investigations—to regularly monitor station nuclear safety culture.
d. Leaders support and participate in candid assessments of
workplace attitudes and nuclear safety culture and act on issues that affect trust in management or detract from a positive nuclear safety culture.
LA.8 Leader Behaviors: Leaders exhibit behaviors that set the standard for
safety. Behavior Examples: a. Leaders "walk the talk," modeling the correct behaviors, especially
when resolving apparent conflicts between nuclear safety and production.
b. Leaders act promptly when a nuclear safety issue is raised to
ensure it is understood and appropriately addressed.
INPO 12-012, Revision 1
c. Leaders maintain high standards of personal conduct that promote
all aspects of a positive nuclear safety culture.
d. Leaders demonstrate interest in plant operations and actively seek
out the opinions and concerns of workers at all levels.
e. Leaders encourage personnel to challenge unsafe behavior and
unsafe conditions, and they support personnel who stop plant activities for safety reasons.
f. Leaders motivate others to practice positive nuclear safety culture
DM. Decision-Making
Decisions that support or affect nuclear safety are systematic, rigorous, and
thorough. Operators are vested with the authority and understand the
expectation, when faced with unexpected or uncertain conditions, to place the
plant in a safe condition. Senior leaders support and reinforce conservative
decisions.
Attributes:
DM.1 Consistent Process: Individuals use a consistent, systematic approach
to make decisions. Risk insights are incorporated as appropriate.
Behavior Examples: a. The organization establishes a well-defined decision-making
process, with variations allowed for the complexity of the issue being decided.
b. Individuals demonstrate an understanding of the decision-making
process and use it consistently.
c. Leaders seek inputs from different work groups or organizations as
appropriate when making safety- or risk-significant decisions.
d. When previous operational decisions are called into question by
new facts, leaders reevaluate these decisions to ensure they remain appropriate.
e. The organization uses the results of effectiveness reviews to
improve future decisions.
DM.2 Conservative Bias: Individuals use decision-making practices that
emphasize prudent choices over those that are simply allowable. A proposed action is determined to be safe in order to proceed, rather than unsafe in order to stop.
INPO 12-012, Revision 1
Behavior Examples: a. Managers ensure that conservative assumptions are used when
determining whether emergent or unscheduled work can be conducted safely.
b. Leaders take a conservative approach to decision-making,
particularly when information is incomplete or conditions are unusual.
c. Leaders consider long-term consequences when determining how
to resolve emergent concerns.
d. Managers take timely action to address degraded conditions
commensurate with their safety significance.
e. Executives and senior managers reinforce the expectation that the
reactor will be shut down when procedurally required, when the margin for safe operation has degraded unacceptably, or when the condition of the reactor is uncertain. Managers implement this expectation.
f. Individuals do not rationalize assumptions for the sake of
completing a task.
DM.3 Accountability for Decisions: Single-point accountability is
maintained for nuclear safety decisions.
Behavior Examples: a. The on-shift licensed operators have the authority and
responsibility to place the plant in a safe condition when faced with unexpected or uncertain conditions.
b. A designated, on-shift licensed senior reactor operator has the
authority and responsibility to determine equipment operability.
c. Managers maintain single-point accountability for important safety
d. The organization ensures that important nuclear safety decisions
are made by the correct person at the lowest appropriate level.
WE. Respectful Work Environment
Trust and respect permeate the organization. A high level of trust is
established in the organization, fostered, in part, through timely and accurate
communication. Differing professional opinions are encouraged, discussed, and
resolved in a timely manner. Employees are informed of steps taken in response
to their concerns.
INPO 12-012, Revision 1
WE.1 Respect is Evident: Everyone is treated with dignity and respect.
Behavior Examples: a. The organization regards individuals and their professional
capabilities and experiences as its most valuable asset.
b. Individuals at all levels of the organization treat each other with
dignity and respect.
c. Individuals treat each other with respect within and between work
d. Individuals do not demonstrate or tolerate bullying or humiliating
e. Leaders monitor for behaviors that can have a negative impact on
the work environment and address them promptly.
f. Leaders ensure policies and expectations are enforced fairly and
consistently for individuals at all levels of the organization.
g. Individuals treat decision-makers with respect, even when they
disagree with a decision.
h. Leaders ensure facilities are conducive to a productive work
environment and housekeeping is maintained.
WE.2 Opinions are Valued: Individuals are encouraged to voice concerns,
provide suggestions, and raise questions. Differing opinions are respected. Behavior Examples: a. The organization encourages individuals to offer ideas, concerns,
suggestions, differing opinions, and questions to help identify and solve problems.
b. Leaders are receptive to ideas, concerns, suggestions, differing
opinions, and questions.
c. The organization promotes robust discussions, recognizing that
differing opinions are a natural result of differences in expertise and experience.
d. Individuals value the insights and perspectives provided by quality
assurance, the employee concerns program, and independent oversight organization personnel.
INPO 12-012, Revision 1
WE.3 High Level of Trust: Trust is fostered among individuals and work
groups throughout the organization. Behavior Examples: a. Leaders promote collaboration among work groups.
b. Leaders respond to questions and concerns in an open and honest
c. Leaders, sensitive to the negative impact of a lack of information,
share important information in an open, honest, and timely manner such that trust is maintained.
d. Leaders ensure that plant status and important work milestones are
communicated throughout the organization.
e. Leaders acknowledge positive performance and address negative
performance promptly and directly with the individual involved. Confidentiality is maintained as appropriate.
f. Leaders welcome performance feedback from throughout the
organization and modify their behavior when appropriate.
WE.4 Conflict Resolution: Fair and objective methods are used to resolve
conflicts. Behavior Examples: a. The organization implements processes to ensure fair and objective
resolution of conflicts and differing views.
b. Leaders ensure conflicts are resolved in a balanced, equitable, and
consistent manner, even when outside of defined processes.
c. Individuals have confidence that conflicts will be resolved
respectfully and professionally.
INPO 12-012, Revision 1
Management Systems
Continuous Learning
Opportunities to learn about ways to ensure safety are sought out and
implemented. Operating experience is highly valued, and the capacity to learn
from experience is well developed. Training, self-assessments, and benchmarking
are used to stimulate learning and improve performance. Nuclear safety is kept
under constant scrutiny through a variety of monitoring techniques, some of
which provide an independent "fresh look."
CL.1 Operating Experience: The organization systematically and
effectively collects, evaluates, and implements relevant internal and external operating experience in a timely manner. Behavior Examples: a. A process is in place to ensure a thorough review of operating
experience provided by internal and external sources.
b. Operating experience is implemented and institutionalized
effectively through changes to station processes, procedures, equipment, and training programs.
c. Operating experience is used to understand equipment, operational,
and industry challenges and to adopt new ideas to improve performance.
d. Operating experience is used to support daily work functions, with
emphasis on the possibility that "it could happen here."
e. Station operating experience is shared in a timely manner.
CL.2 Self-Assessment: The organization routinely conducts self-critical and
objective assessments of its programs and practices. Behavior Examples: a. Independent and self- assessments, including nuclear safety culture
assessments, are thorough and effective and are used as a basis for improvements.
b. The organization values the insights and perspectives assessments
c. Self-assessments are performed on a variety of topics, including
the self-assessment process itself.
INPO 12-012, Revision 1
d. Self-assessments are performed at a regular frequency and provide
objective, comprehensive, and self-critical information that drive corrective actions.
e. Targeted self-assessments are performed when a more thorough
understanding of an issue is required.
f. A balanced approach of self-assessments and independent
oversight is used and periodically adjusted based on changing needs.
g. Self-assessment teams include individual contributors and leaders
from within the organization and from external organizations when appropriate.
CL.3 Benchmarking: The organization learns from other organizations to
continuously improve knowledge, skills, and safety performance. Behavior Examples: a. The organization uses benchmarking as an avenue for acquiring
innovative ideas to improve nuclear safety.
b. The organization participates in benchmarking activities with other
nuclear and nonnuclear facilities.
c. The organization seeks out best practices by using benchmarking
to understand how others perform the same functions.
d. The organization uses benchmarking to compare station standards
to the industry and to make adjustments to improve performance.
e. Individual contributors are actively involved in benchmarking.
CL.4 Training: The organization provides training and ensures knowledge
transfer to maintain a knowledgeable, technically competent workforce and instill nuclear safety values. Behavior Examples: a. The organization fosters an environment in which individuals
value and seek continuous learning opportunities.
b. Individuals, including supplemental workers, are adequately
trained to ensure technical competency and an understanding of standards and work requirements.
c. Individuals master reactor and power plant fundamentals to
establish a solid foundation for sound decisions and behaviors.
d. The organization develops and effectively implements knowledge
transfer and knowledge retention strategies.
INPO 12-012, Revision 1
e. Knowledge transfer and knowledge retention strategies are applied
to capture the knowledge and skill of experienced individuals to advance the knowledge and skill of less experienced individuals.
f. Leadership and management skills are systematically developed.
g. Training is developed and continuously improved using input and
feedback from individual contributors and subject-matter experts.
h. Executives obtain the training necessary to understand basic plant
operation and the relationships between major functions and organizations.
Problem Identification and Resolution
Issues potentially impacting safety are promptly identified, fully evaluated,
and promptly addressed and corrected commensurate with their
significance. Identification and resolution of a broad spectrum of problems,
including organizational issues, are used to strengthen safety and improve
performance.
Attributes:
Identification: The organization implements a corrective action program with a low threshold for identifying issues. Individuals identify issues completely, accurately, and in a timely manner in accordance with the program. Behavior Examples: a. Individuals recognize deviations from standards.
b. Individuals understand how to enter issues into the corrective
c. Individuals ensure that issues, problems, degraded conditions, and
near misses are promptly reported and documented in the corrective action program at a low threshold.
d. Individuals describe the issues entered in the corrective action
program in sufficient detail to ensure they can be appropriately prioritized, trended, and assigned for resolution.
Evaluation: The organization thoroughly evaluates problems to ensure that resolutions address causes and extents of conditions commensurate with their safety significance.
INPO 12-012, Revision 1
Behavior Examples: a. Issues are properly classified, prioritized, and evaluated according
to their safety significance.
b. Operability and reportability determinations are developed when
c. Apparent and root cause investigations identify primary and
contributing causal factors as required.
d. Extent-of-condition and extent-of-cause evaluations are completed
in a timely manner, commensurate with the safety significance of the issue.
e. Issues are investigated thoroughly according to their safety
f. Root cause analyses are rigorously applied to identify and correct
the fundamental cause of significant issues.
g. The underlying organizational and safety culture contributors to
issues are evaluated thoroughly and are given the necessary time and resources to be clearly understood.
h. Cause analyses identify and understand the bases for decisions that
contributed to issues.
i. Managers conduct effectiveness reviews of significant corrective
actions to ensure that the resolution addressed the causes effectively.
Resolution: The organization takes effective corrective actions to address issues in a timely manner commensurate with their safety significance. Behavior Examples: a. Corrective actions are completed in a timely manner.
b. Deferrals of corrective actions are minimized. When required, due
dates are extended using an established process that appropriately considers safety significance.
c. Appropriate interim corrective actions are taken to mitigate issues
while more fundamental causes are being assessed.
d. Corrective actions resolve and correct the identified issues,
including causes and extents of conditions.
e. Corrective actions prevent the recurrence of significant conditions
adverse to quality.
INPO 12-012, Revision 1
f. Trends in safety performance indicators are acted on to resolve
Trending: The organization periodically analyzes information from the corrective action program and other assessments in the aggregate to identify programmatic and common cause issues. Behavior Examples: a. The organization develops indicators that monitor both equipment
and organizational performance, including safety culture.
b. Managers use indicators that provide an accurate representation of
performance and early indications of declining trends.
c. Managers routinely challenge the organization's understanding of
declining trends.
d. Organizational and departmental trend reviews are completed in a
timely manner in accordance with program expectations.
Environment for Raising Concerns
A safety-conscious work environment (SCWE) is maintained where
personnel feel free to raise safety concerns without fear of retaliation,
intimidation, harassment, or discrimination. The station creates, maintains,
and evaluates policies and processes that allow personnel to raise concerns freely.
Attributes:
RC.1 SCWE Policy: The organization effectively implements a policy that
supports individuals' rights and responsibilities to raise safety concerns and does not tolerate harassment, intimidation, retaliation, or discrimination for doing so. Behavior Examples: a. Individuals feel free to raise nuclear safety concerns without fear
of retribution, with confidence that their concerns will be addressed.
b. Executives and senior managers set and reinforce expectations for
establishing and maintaining a safety-conscious work environment.
c. Policies and procedures reinforce that individuals have the right
and responsibility to raise nuclear safety concerns.
d. Policies and procedures define the responsibilities of leaders to
create an environment in which individuals feel free to raise safety concerns.
INPO 12-012, Revision 1
e. Policies and procedures establish the expectation that leaders will
respond in a respectful manner and provide timely feedback to the individual raising the concern.
f. Leaders are trained to take ownership when receiving and
responding to concerns, recognizing confidentiality if appropriate, and ensuring they are adequately addressed in a timely manner.
g. Individuals are trained that behaviors or actions that could prevent
concerns from being raised, including harassment, intimidation, retaliation, or discrimination, will not be tolerated and are violations of law and policy.
h. All claims of retaliation are investigated and any necessary
corrective actions are taken in a timely manner, including actions to mitigate any potential chilling effect.
RC.2 Alternate Process for Raising Concerns: The organization effectively
implements a process for raising and resolving concerns that is independent of line management influence. Safety issues may be raised in confidence and are resolved in a timely and effective manner. Behavior Examples: a. Executives establish, support, and promote the use of alternative
processes for raising concerns and ensure corrective actions are taken.
b. Leaders understand their role in supporting alternate processes for
raising concerns.
c. Processes for raising concerns or resolving differing professional
opinions that are alternatives to the corrective action program and operate outside the influence of the management chain are communicated and accessible to individuals.
d. Alternative processes are independent, include an option to raise
concerns confidentially, and ensure these concerns are appropriately resolved in a timely manner.
e. Individuals receive feedback in a timely manner.
f. Individuals have confidence that issues raised will be appropriately
g. Individuals assigned to respond to concerns have the appropriate
INPO 12-012, Revision 1
WP. Work Processes
The process of planning and controlling work activities is implemented so
that safety is maintained. Work management is a deliberate process in which
work is identified, selected, planned, scheduled, executed, closed, and critiqued.
The entire organization is involved in and fully supports the process.
Attributes:
WP.1 Work Management: The organization implements a process of
planning, controlling, and executing work activities such that nuclear safety is the overriding priority. The work process includes the identification and management of risk commensurate to the work. Behavior Examples: a. Work is effectively planned and executed by incorporating risk
insights, job-site conditions, and the need for coordination with different groups or job activities.
b. The work process appropriately prioritizes work and incorporates
contingency plans, compensatory actions, and abort criteria as needed.
c. Leaders consider the impact of changes to the work scope and the
need to keep personnel apprised of the work status.
d. The work process ensures individuals are aware of the plant status,
the nuclear safety risks associated with work in the field, and other parallel station activities.
e. Insights from probabilistic risk assessments are considered in daily
work activities and change processes.
f. Work activities are coordinated to address conflicting or changing
priorities across the whole spectrum of activities contributing to nuclear safety.
g. The work process limits temporary modifications.
WP.2 Design Margins: The organization operates and maintains equipment
within design margins. Margins are carefully guarded and changed only through a systematic and rigorous process. Special attention is placed on maintaining fission product barriers, defense-in-depth, and safety-related equipment. Behavior Examples: a. The work process supports nuclear safety and the maintenance of
design margins by minimizing long-standing equipment issues,
INPO 12-012, Revision 1
preventive maintenance deferrals, and maintenance and engineering backlogs.
b. The work process ensures focus on maintaining fission product
barriers, defense-in-depth, and safety-related equipment.
c. Design and operating margins are carefully guarded and changed
only with great thought and care.
d. Safety-related equipment is operated and maintained well within
design requirements.
WP.3 Documentation: The organization creates and maintains complete,
accurate, and up-to-date documentation. Behavior Examples: a. Plant activities are governed by comprehensive, high-quality
programs, processes, and procedures.
b. Design documentation, procedures, and work packages are
complete, thorough, accurate, and current.
c. Components are labeled clearly, consistently, and accurately.
d. The backlog of document changes is understood, prioritized, and
actively managed to ensure quality.
WP.4 Procedure Adherence: Individuals follow processes, procedures, and
work instructions. Behavior Examples: a. Individuals follow procedures.
b. Individuals understand and use human error reduction techniques.
c. Individuals review procedures and instructions prior to work to
validate that they are appropriate for the scope of work and that required changes are completed prior to implementation.
d. Individuals manipulate plant equipment only when appropriately
authorized and directed by approved plant procedures or work instructions.
e. Individuals ensure the statuses of work activities are properly
INPO 12-012, Revision 1
The table below is from
Traits of a Healthy Nuclear Safety Culture Addendum II: Cross-References.
INPO PRINCIPLES TO TRAITS
INPO Principle
Everyone is personally responsible for
Personal Accountability
Leaders demonstrate commitment to
Leadership Safety Values and Actions
Trust permeates the organization.
Effective Safety Communication Respectful Work Environment Environment for Raising Concerns
Decision-making reflects safety first.
Nuclear technology is recognized as
special and unique.
A questioning attitude is cultivated.
Questioning Attitude
Organizational learning is embraced.
Continuous Learning
Problem Identification and Resolution
Nuclear safety undergoes constant
Continuous Learning
Problem Identification and Resolution
INPO 12-012, Revision 1
This page is intentionally blank.
INPO 12-012, Revision 1
ACKNOWLEDGEMENTS
The following individuals participated in advisory groups that developed the traits and attributes in this document.
Jeffrey B. Archie
Pierre Francois Gest
Senior Vice President and Chief Nuclear Officer
Senior Safety Officer
South Carolina Electric & Gas Company
Operational Safety Section
International Atomic Energy Agency
Ronald A. Barnes
Director, Nuclear Regulatory Affairs
Edward D. Halpin
Arizona Public Service Company
Senior Vice President and Chief Nuclear Officer
Pacific Gas and Electric Company
Elizabeth Beswick
Nuclear Professionalism Consultant Nuclear
General Manager & Group Leader
Japan Nuclear Technology Institute
Manager, Management System Department
Manager, Corporate Nuclear Oversight
Progress Energy, Inc.
Albert R. Hochevar
Deputy Director, OR Team Leaders
Energy Strategists Consultancy Limited
Institute of Nuclear Power Operations
Senior Director, Safety Focused Regulation
WANO Paris Center
Nuclear Energy Institute
Randall K. Edington
William R. Illing
Executive Vice President and Chief Nuclear
Senior Program Manager
Institute of Nuclear Power Operations
Arizona Public Service Company
Safety Standards Advisor
Director, Nuclear Oversight
Safety and Security Coordination
PSEG Nuclear LLC
International Atomic Energy Agency
Jose Manuel Diaz Francisco
Communication and Safety Coordinator
Human Factors Specialist
Office of Nuclear Reactor Regulation
U.S. Nuclear Regulatory Commission
David F. Garchow
Vice President, Plant Technical Support
Institute of Nuclear Power Operations
Senior Safety Specialist
Division of Nuclear Installation Safety
Billie Garde, Esq.
Department of Nuclear Safety and Security
International Atomic Energy Agency
Clifford & Garde, LLP
G. Kenneth Koves, Ph.D.
Principal Program Manager
Licensing Manager
Institute of Nuclear Power Operations
Exelon Corporation
INPO 12-012, Revision 1
Johann Kritzinger
Philip K. Russell
Corporate Consultant: Human Performance
Nuclear Operating Unit
Institute of Nuclear Power Operations
Eskom Holdings SOC Ltd
Valérie Lagrange
Reactor Inspector
Safety Management & Human Factors Advisor
Nuclear Operation Division
U.S. Nuclear Regulatory Commission
Electricité de France
Chief, Health Physics and Human Performance
Vice President, Assistance
Institute of Nuclear Power Operations
Office of Nuclear Reactor Regulation
U.S. Nuclear Regulatory Commission
Human Factors Engineer
Office of Nuclear Reactor Regulation
Senior Safety Culture Program Manager
U.S. Nuclear Regulatory Commission
Office of Enforcement
U.S. Nuclear Regulatory Commission
Stephanie Morrow, Ph.D.
Human Factors Analyst
Office of Nuclear Regulatory Research
Senior Director, Safety Focused Regulation
U.S. Nuclear Regulatory Commission
Nuclear Energy Institute
Kevin J. Mulligan
Preston D. Swafford
Vice President, Operations Support
Executive Vice President and Chief Nuclear
Tennessee Valley Authority
Michael J. Pacilio
President and Chief Nuclear Officer Exelon
Human Performance, RQH and Safety Culture
Exelon Corporation
Vattenfall AB; Ringhals NPP
Chief, Technical Support and Assessment
Engineer, Performance Monitoring Section
Safety and Compliance Department
U.S. Nuclear Regulatory Commission
S.N. Nuclearelectrica
Prognoz - Obninsk Science Research Center
Andrew J. Vomastek
Senior Reactor Inspector
Fleet Manager, Dominion Nuclear Employee
Concerns Programs
U.S. Nuclear Regulatory Commission
Dominion Generation
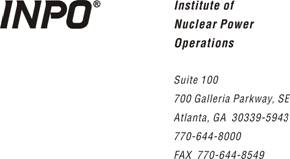
Source: http://nuclearsafety.info/wp-content/uploads/2010/07/Traits-of-a-Healthy-Nuclear-Safety-Culture-INPO-12-012-rev.1-Apr2013.pdf
Nutrient Profile of Nutritional Support for CNS Disorders Copyright © January, 2001 Truehope Nutritional Support Ltd. A Non-Profit Company Revised August, 2006 Table of Contents 1. Nutrient Insufficiency Theory.2 2. Nutrient Profile .3 3. Possible Interfering Factors.28 4. Conclusion .32 Preface There are many good reasons to suspect that nutrition, or the lack of it, may be the root cause of many of our chronic illnesses, including disorders of the central nervous system. Small population pockets in a few places around the world such as the Hunza population in Kashmir, the Georgians from the southern Soviet Union and the mountain village of Vilcabamba in Ecuador are reported to live much longer and remain more vigorous in old age than in most modern societies.1 The Japanese island of Okinawa also shares a similar reputation, and like these other populations enjoys life with little or no chronic or mental illness. One has to ask why such a phenomenon occurs. The only common factor shared by these diverse populations seems to be the incredible macro and micronutrient density of their foods and water coupled with rich soils, which do not suffer from depletion. These populations ingest many times the macro and microelement levels ingested by the average North American. Around the world, soil depletion of nutrients is at a very high level. The statistics from the 1992 Earth Summit Report indicate that 85% of the minerals present in North American topsoils 100 years ago are no longer present. This correlates with the findings of Anne-Marie Mayer, PhD who reported that the general decline of nutrients in 40 foods examined over a 50-year period of analysis in the UK reached a peak of an 81% decrease for a single element.2 This decrease in nutrient density in our foods could easily have been predicted; as for hundreds of years the principle elements replenished in farm soils have been only nitrogen, phosphorus and potassium. The over-processing of foods has also, no doubt, contributed to the problem of low nutrient intake. White flour, for instance, contains only 7% of the trace elements found in whole-wheat flour.3 Another factor which figures into this equation is the load put on body resources to metabolize and eliminate environmental contaminants and pollutants. Various chemicals including herbicide and pesticide exposure, not to mention the numerous airborne toxins that our bodies are constantly exposed to, put an overload on body metabolic processes and resources to counter such exposure.
a bayeux.fr un été à Bayeux Les Médiévales : Un nouveau complexe de loisirs avenue de la Vallée des Près Un jardin pour Salomé Le 19 mai dernier a été inauguré le Jardin de Salomé, baptisé en hommage à Salomé Girard, jeune Bayeusaine victime de l'attentat survenu à EmbEllir la villE